Технология CFC
Технология коэкструзии композитного волокна СFC (Composite Filament Co-extrusion) предназначена для изготовления сверхпрочных изделий сложной формы и внутренней структуры из термопластов, армированных непрерывными композитными волокнами на основе углеродных жгутов и термореактивного связующего.
Описание
3D принтеры компании Анизопринт представляют собой устройства для коэкструзии двухматричного композита, что добавляет возможность создания деталей для высоконагруженных применений к традиционной технологии FDM/FFF. Линейка компании на данный момент представлена следующими модификациями принтеров Composer: A2, A3 и A4.
Для подготовки 3D печати используется специализированное программное обеспечение Anisoprint Aura (входит в комплект поставки). Anisoprint Aura позволяет подготовить 3D-модель для печати, оптимизировать и настроить схему армирования и объемную долю армирующего волокна в разных частях детали. Использование специализированного ПО дает возможность печатать мелкие элементы детали при помощи дополнительного сопла без армирования. Хранение, обработка и запуск печати производится с локального компьютера, что позволяет сохранять конфиденциальности и безопасности разрабатываемых моделей.
Для печати с армированием используется специально подготовленное патентованное композитное волокно Anisoprint CCF и Anisoprint CBF, обеспечивающие качественную адгезию к пластику и пропитку волокна.
Использование технологии при производстве деталей для аэрокосмической, автомобильной промышленности, станко- и судостроения, позволит снизить массу детали в 2-3 раза по сравнению с традиционными технологиями и повысить экономическую эффективность. Технология аддитивная, полностью автоматизированная, работает на основе цифровых моделей.
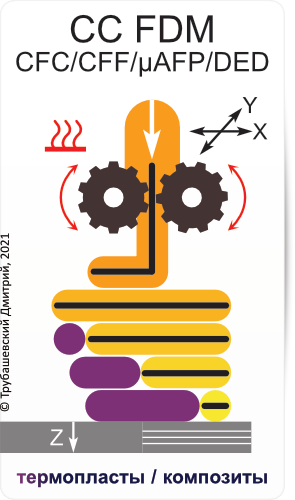
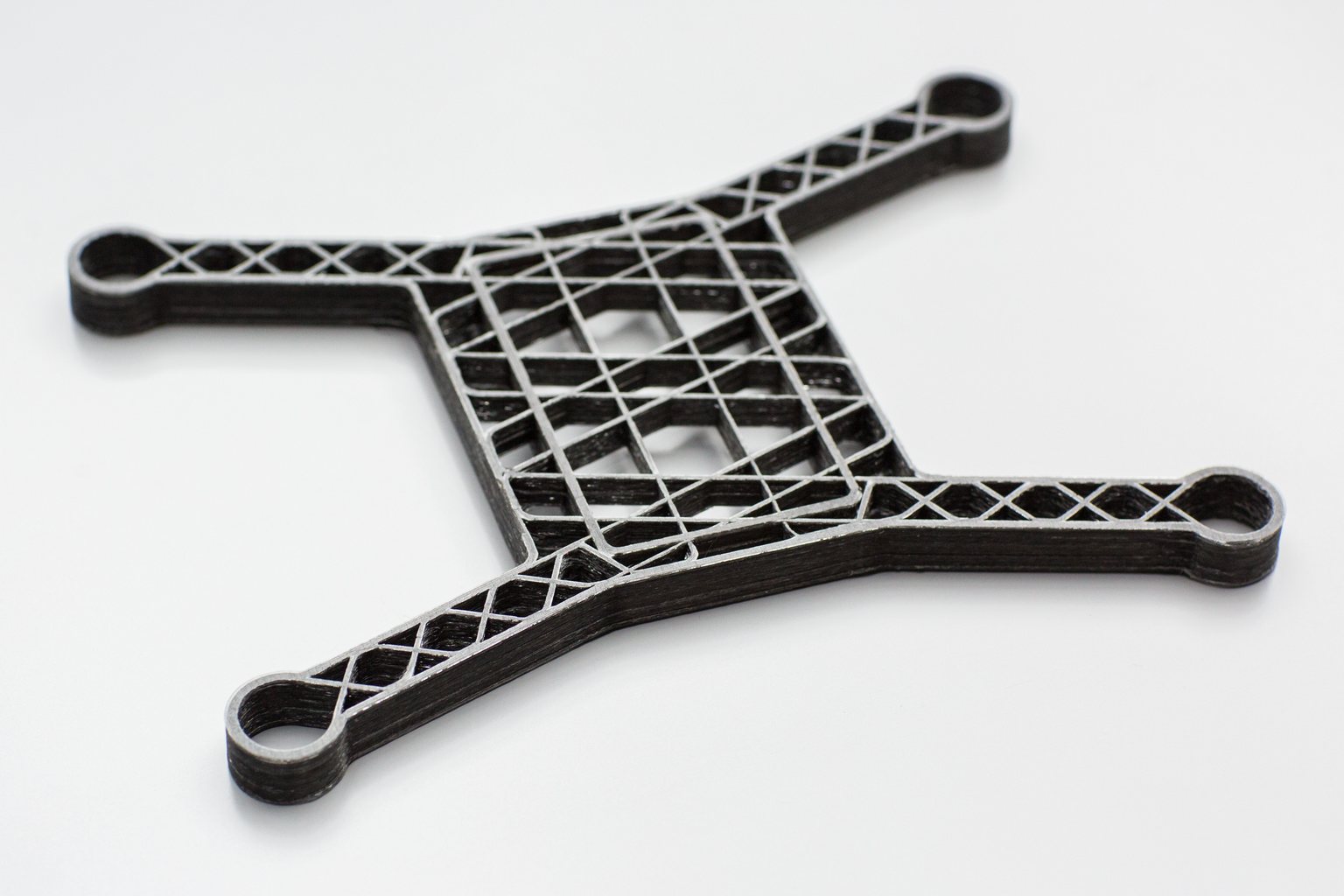
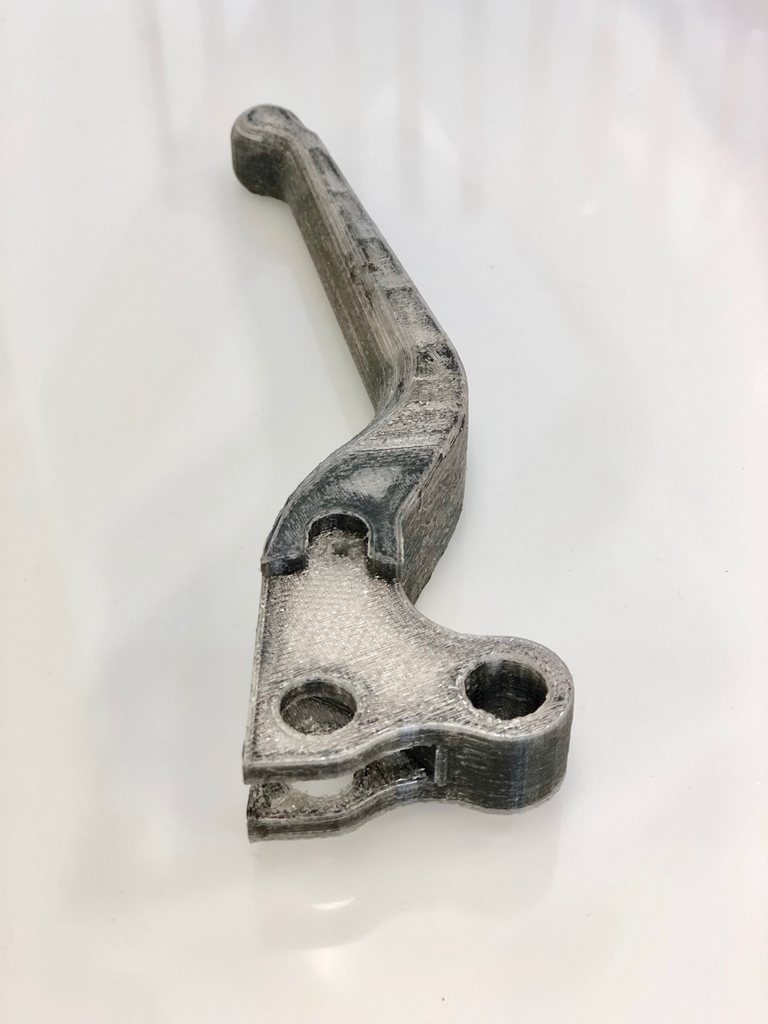
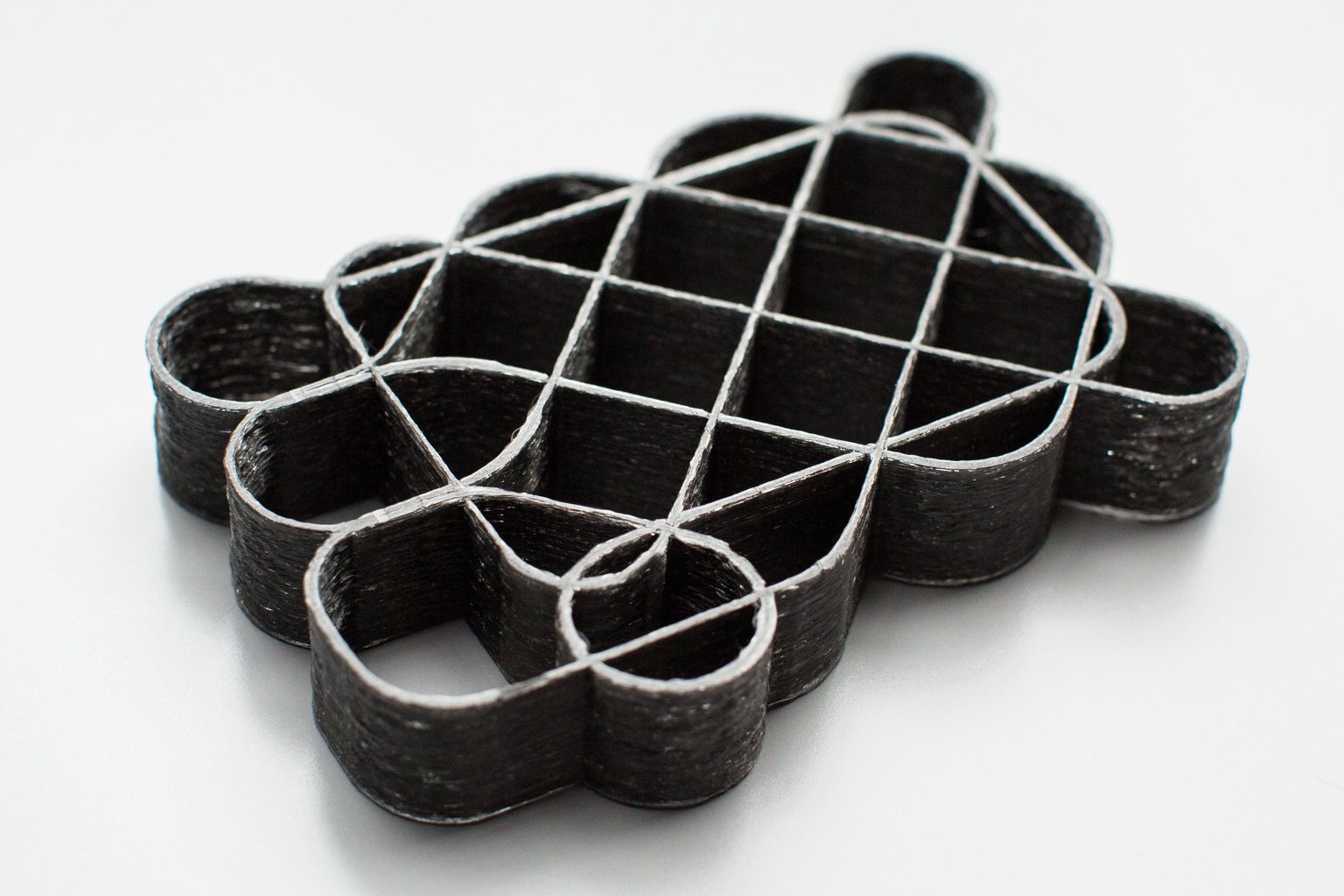
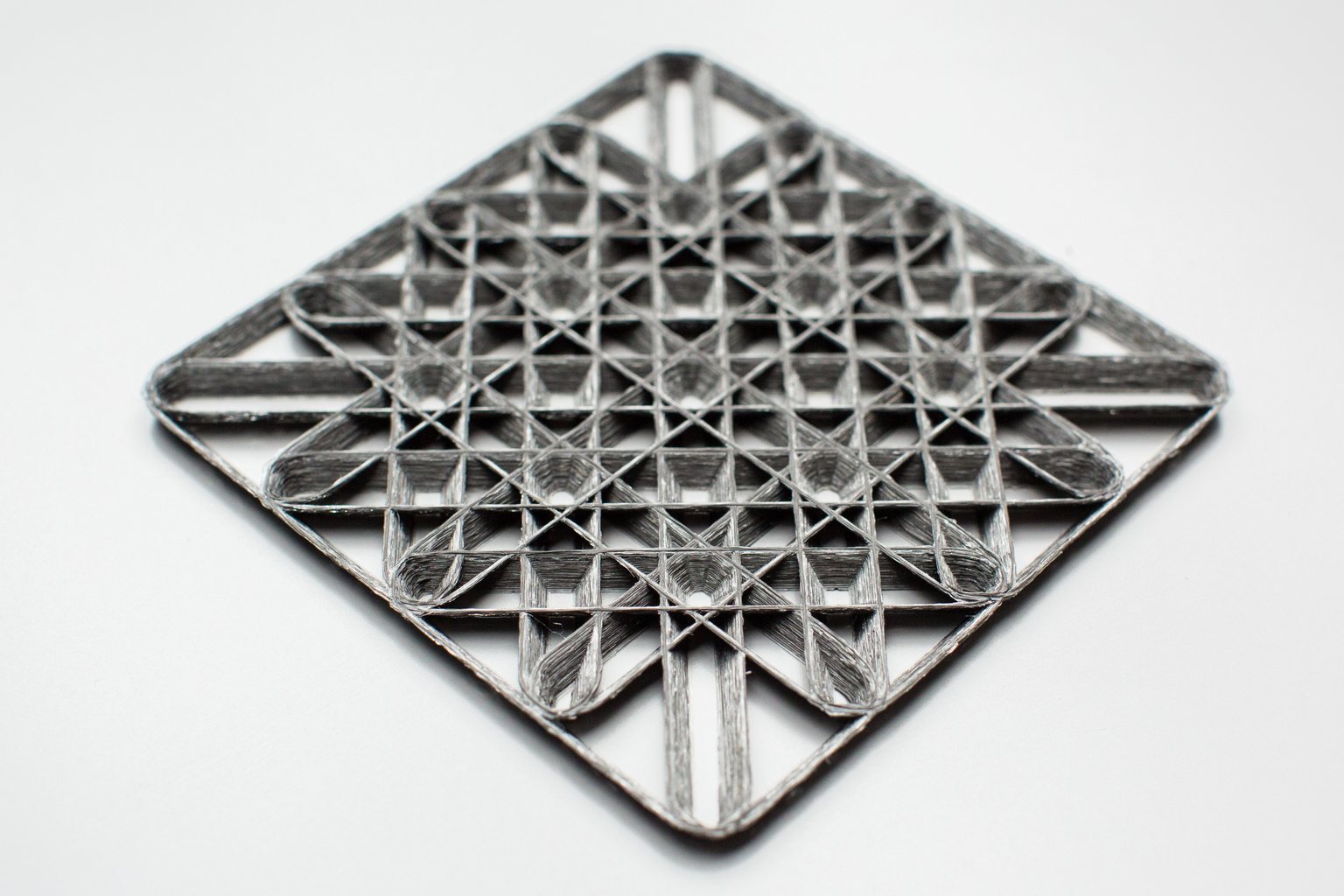
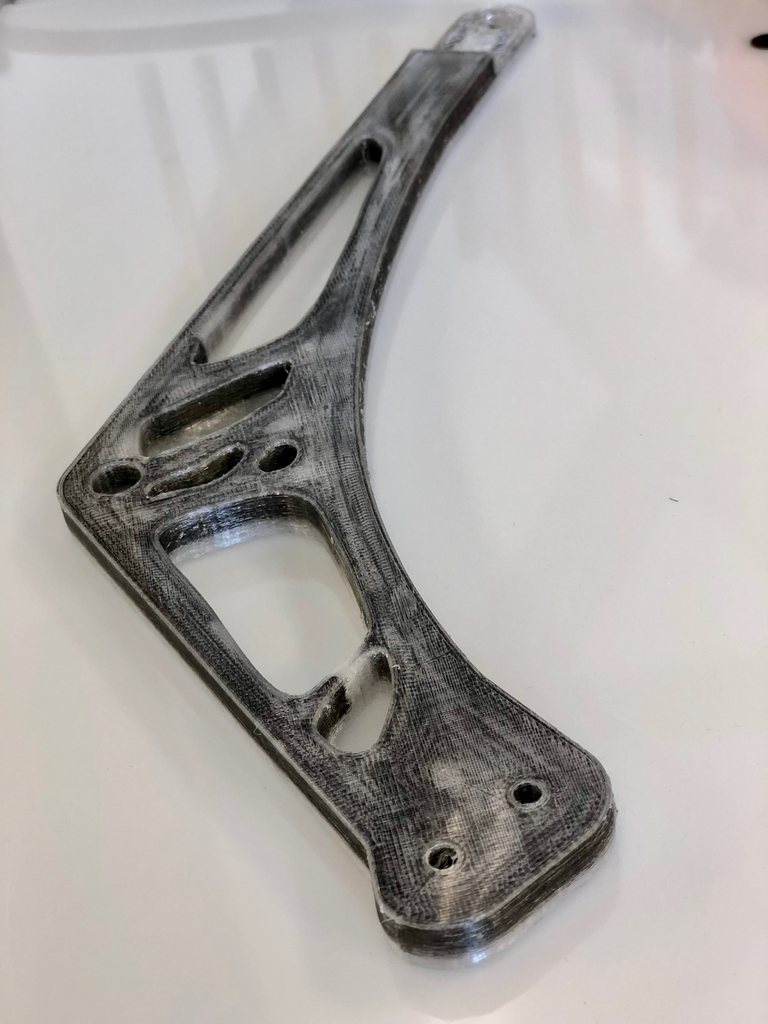
Преимущества
- в 20 раз прочнее обычного пластика;
- в 1,5 раза прочнее алюминия;
- в 7 раз легче стали;
- стоимость оборудования в 10 раз меньше чем при лазерном спекании;
- потребление энергии в 20 раз меньше;
- стоимость 1 куб. см. материала в 5 раз меньше чем у металлических порошков;
- неограниченные возможности для оптимизации;
- одностадийный процесс;
- не требуется технологическая оснастка;
- коэффициент использования материала – 100%.