АТ: парк машин растет, специалисты — в дефиците
Итоги выставки и конференции по экосистеме аддитивных технологий «3DFab + Print Russia 2019»
В конце января в Экспоцентре на Красной Пресне состоялась третья Международная специализированная конференция по аддитивным технологиям в промышленности «3DFab + Print Russia 2019». Традиционно 3DFab + Print Russia проводился в рамках ведущей специализированной выставки пластмасс и каучука Interplastica, организует которую Messe Dusseldorf Moscow. Организатором конференции 3DFab + Print Russia 2019 с акцентом на использование аддитивных технологий в различных отраслях промышленности стало ООО «Современное оборудование» Группы компаний «Солвер».
Для отечественных «аддитивщиков» этот форум можно считать одним из главных отраслевых мероприятий с точки зрения расстановки акцентов. Несмотря на субъективные и объективные факторы, сдерживающие развитие 3D-печати в российской промышленности, этот поезд, что называется, уже не остановить. Аддитивные технологии получают все большее распространение в различных отраслях промышленности. Дмитрий Трубашевский, директор по продажам ООО «Современное оборудование», входящего в ГК «Солвер», уверен, что стремительный поток в виде знаний, новых технологий в 3D-печати, нового оборудования и материалов подточит камень консерватизма и некомпетентности. И в итоге АТ-методы наконец займут подобающее место в отечественной индустрии.
— Дмитрий, пожалуйста, поделитесь вашими впечатлениями организатора и участника третьей по счету конференции «3DFab + Print Russia». Сохраняется ли устойчивый интерес Messe Duesseldorf к российскому АТ рынку?
— В первую очередь я благодарен главным организаторам выставки – компании Messe Duesseldorf Moscow за доверие и эффективное сотрудничество, Они полагают, что российский АТ рынок является весьма перспективным. Наша компания «Современное оборудование» подбирала спикеров и экспонентов, модерировала конференцию. Конечно, при этом мы, как и другие участвовавшие в выставке отечественные инновационные компании, продвигали здесь и свои уникальные решения, и подходы.
— Общаясь с участниками конференции, убеждаешься, что далеко не все оптимистично оценивают перспективы развития АТ в России. У многих машиностроителей проскальзывает определенная разочарованность из-за неудачного опыта использования аддитивных машин, низкого качества порошков, необходимости использования токарно-фрезерного оборудования для дальнейшего доведения изделий полученных с помощью АТ и т.д. В общем, ожидания не оправдались, и теперь приходится снимать розовые очки?
— Эту проблему следует рассматривать в иной плоскости. Действительно существуют технические сложности работы с металлопорошками. Есть и трудности, связанные с механическими свойствами конструкционных материалов. Но основная проблема — недостаток у российских производственников знаний и навыков для их преодоления. И это не столько их вина, сколько беда: когда, несколько лет назад, АТ-технологии у нас только начинали внедрять, во многих компаниях, особенно с госучастием, это внедрение практически свелось к освоению средств на закупку соответствующего оборудования, считалось, что, мол, остальное само приложится. Инерция такого подхода очень сильна, до сих пор у нас есть поставщики, продающие предприятиям оборудование без полноценного внедрения у покупателя технологий, без качественного обучения его специалистов. Тогда как эффективность применения АТ обеспечивается целым комплексом составляющих: это и полноценная подготовка специалистов, и внедрение технологии в соответствии с потребностями заказчика, и постпродажный сервис и т.д. Интернет-магазины, реселлеры оборудования, компании, именующие себя интеграторами — все заявляют о готовности предоставить все необходимое для полного производственного цикла, но на деле это получается не всегда и не у всех. К сожалению, предприятия вынуждены прибегать к помощи зарубежных компаний, либо искать и договариваться с теми немногими локальными игроками, кто «в теме».
Поэтому причина некоторого разочарования в АТ не в том, что 3D-принтеры не работают или материалы некачественные, хотя и это очень важно. Просто либо оборудование внедрено не совсем корректно, либо заказчик не до конца понимает его применимость для своих задач, либо заказчик стал пасовать перед сложными вопросами сертификации конечной продукции. В результате вместо 100% его возможностей не используется и 10%. Чиновники, руководство предприятий, инженеры и операторы оборудования должны быть мотивированы на полное использование инновационного оборудования для улучшения текущих экономических показателей цехов или заводов.
Но есть и положительные примеры, например в «ОДК-Авиадвигатель» сформировалась команда, которая на протяжении восьми лет занимается изучением порошков, техпроцессов, технологий и созданием готовых, в том числе ремонтных, изделий. И лишь сравнительно недавно они получили удовлетворительный результат после многолетней работы. То есть полноценно «прочувствовать» технологию, решить вопросы с сертификацией, и начать использовать аддитивные технологии на ответственных задачах можно в среднем за 5-8 лет. Хватит ли терпения у других компаний-потребителей? Сегодняшние реалии у многих из них таковы: приобрели 3D-принтеры, поставили в опрятном цехе, благополучно отчитались об освоении средств и всё. Ну а польза может быть только у тех, кто набрался терпения, чтобы разобраться в процессах, обучил персонал, проанализировал рынок, составил бизнес-план, благодаря которому принтер загружен работой в режиме 24/7.
— На выставке «3DFab+Print Russia 2019» были представлены не только производители 3D-принтеров и порошков, но и ряд сервисных компаний, предоставляющих услуги по 3D-печати прототипов, заготовок, оснастки. Как вы считаете, какой путь развития АТ в России выглядит более перспективным: расширение рынка такого рода услуг либо все же трехмерная печать готовых изделий?
— Действительно, существует несколько направлений АТ. Прототипирование развивается стремительно и, практически не зависит от перечисленных нами негативных факторов. Для безответственного прототипирования может подойти самый дешёвый принтер, стоимостью в несколько сотен тысяч рублей. Недавно специалисты компании Stratasys провели анализ рынка и пришли к выводу, что более 50% продукции, выпускаемой на современных 3D-принтерах, является прототипами. Поэтому задача быстрого прототипирования может быть решена на всех без исключения машинах. Но сейчас промышленность больше заинтересована в оборудовании, способном печатать качественную оснастку и готовую продукцию. По сути, вопрос оснастки тоже решён, ведь её не нужно сертифицировать. Производство готовой продукции, включающее в себя оборудование и технологию, не может обойтись без сертификации. Это реально сложно реализовать и согласовать в любой стране, в том числе в России. Хотя Запад здесь двигается гораздо быстрее: там есть прорывные методики и огромный опыт, измеряемый десятилетиями. В России же, при том, что многие предприятия обзавелись 3D-принтерами, без специалистов и возможности обучения персонала львиная доля таких производственных мощностей простаивает.
— Если отталкиваться от западного опыта использования АТ в индустрии, то что нам стоило бы у них перенять? Там больше экспериментировали, проводили глубокий анализ? Почему в Европе и в США АТ доверяют гораздо больше и активно замещают революционными технологиями в том числе классическую металлообработку?
— Сегодняшнее лидерство в этом сегменте в западных странах связано в первую очередь с тем, что они были первопроходцами. Понадобилось по крайней мере 15-20 лет, чтобы окончательно понять эти процессы. В той же Германии порошковая технология изучена досконально, вплоть до самого низкого уровня. В своё время к изучению АТ подключались ведущие университеты, например, Институт Фраунгофера (Fraunhofer Institute for Laser Technology ILT). На Западе возможно приобрести любое высокотехнологичное оборудование, в том числе 3D-принтеры, в лизинг на очень выгодных условиях. Россия включилась в освоение и понимание этих технологий совсем недавно, поэтому впору говорить не только о разочаровании, но и об определённом непонимании. Запад смотрит на АТ с прагматической точки зрения — использовать оборудование для изготовления ответственных деталей на коммерческой основе, а уже потом думать о публичном пиаре. В развитых странах сервисные бюро растут, как грибы после дождя, их владельцы не просто уверены, они знают наверняка, что 20-30 единиц оборудования окупится через 2 — 3 года. В России же до сих пор АТ — больше в области чувственно-эмоционального, нежели рационального понимания, закупка 3D-принтеров здесь — нередко просто дань последним модным технологическим трендам. Таким образом оборудования закуплено на многие миллиарды рублей, но функционально поставленные задачи не выполняются. Другое дело, если всю эту инфраструктуру направить в нужное русло, а именно в формирование аддитивных центров, создаваемых не для коммерческих целей, а для подготовки профильных высококлассных специалистов. Но и этого не происходит. Российские вузы в массе своей не располагают хорошим оборудованием для учебного процесса по этому профилю, да и вузовская подготовка недостаточна, чтобы освоить все нюансы АТ. Аддитивные технологии — это теория, практика, современная инфраструктура, время и бесконечные эксперименты. «ВИАМ», «ОДК-Авиадвигатель», «Лазерные системы», «Титан-Авангард» (ТМ Additive Solutions), «Лазеры и аппаратура», МЦЛТ, ЦНИИТМАШ, «Аддитивные технологии», АО «Центр аддитивных технологий», «Анизопринт», «Эксклюзивные Решения» (ТМ 3DSLA, RussianSLM), Picaso 3D, Total Z, Царь 3D, СПЕЦАВИА, Apis Cor — немногие известные примеры российского успешного проектирования и использования технологий 3D-печати. Пока что на российском рынке АТ — период застоя, отчасти вызванный санкциями, низкой платежеспособностью в стране, как среди населения, так и в среде бизнеса.
— Судя по всему, финансовые трудности отечественного бизнеса — это надолго!
— Тем не менее, именно с частным бизнесом связываются основные надежды на продвижение и развитие АТ в России. Наступает время сервисных компаний, предоставляющих услуги по 3D-печати. Всем понятно, что зарубежное оборудование достаточно дорогое, при этом мало его купить, надо уметь им пользоваться. Некоторые предприятия не могут позволить себе купить новый станок для 3D-печати, но при этом остро нуждаются в прототипе, оснастке или даже в готовом изделии. В связи с этим, у сервисных компаний появляется отличная возможность заработать, взяв на себя полный цикл проектирования и изготовления продукции под ключ, используя все необходимые атрибуты инжиниринга. Отдав бизнес-процесс на аутсорсинг, заказчики существенно экономят не только на площадях и оборудовании, но и на персонале. Думаю, что именно сейчас отечественным сервисным компаниям следует как можно активнее завоевывать рынок. Радует, что, несмотря на все сложности, в «аддитивку» смело устремились молодые предприниматели. У них горят глаза, они готовы свернуть горы. Посмотрите, например, на «Титан-Авангард» (ТМ Additive Solutions): компании — всего год, а они уже собрали рабочий принтер. Понятно, что их труды во многом основаны на тридцатилетнем опыте таких китов, как SLM Solutions, Concept Laser, EOS, но госкомпании собирают свои принтеры до сих пор, а D250 уже печатает. Еще одно перспективное направление, наш ответ MIM-технологиям, заключается в печати изделий из комбинированного материала, состоящего на 85% из мелкодисперсного металлического порошка и на 15% из органического полимера. Материал выдавливается через горячую фильеру, и мы получаем трехмерную «зеленую» модель, затем удаляем полимер, спекаем и подвергаем ее горячему изостатическому прессованию (по необходимости). В итоге мы получаем изделие с любой внутренней геометрией за гораздо меньшие сроки и деньги. Технология не революционная, но, безусловно, прорывная. У создателей этого решения зреет план выхода на российский рынок чуть ли не в этом году. Подобных решений я ждал от российского рынка, потому что проектировать и изготавливать SLM-принтеры, на мой взгляд, не перспективно. По сути, SLM — технология вчерашнего дня, хотя многие эксперты наверняка захотят со мной поспорить. Даже специалисты ВИАМ, будучи стойкими апологетами SLM технологий, все чаще начинают заявлять о других способах АТ.
— Если говорить об имеющихся металлических технологиях, какой метод 3D-печати предпочтительнее: селективное лазерное сплавление SLM или коаксиальная лазерная наплавка LMD?
— Этот вопрос — для интеграторов промышленных решений с применением аддитивных и не аддитивных технологий. Когда компания досконально разбирается в вопросе, нарабатывает опыт в этой сфере, она может рекомендовать для каждого клиента оптимальную технологию или ряд технологий. Нельзя сказать однозначно, какая технология лучше, всё зависит от конкретных задач. Когда к нам обращается клиент, мы следуем классическим постулатам «Солвера»: запрашиваем техническое задание, узнаём пожелания заказчика, его целеполагание в краткосрочной и долгосрочной перспективе, и только после этого начинаем подбирать решение, оптимальное на данный момент и на перспективу. Как правило, повышение эффективности производства следует начинать с программного обеспечения; если с программным обеспечением и автоматизацией вопрос более-менее закрыт, то далее следует рассмотреть внедрение инструментов Бережливого производства, системы менеджмента качества. Если возможности станочного парка достигли максимума — приобретено современное токарно-фрезерное оборудование, а дальнейшего роста производительности нет, то в этом случае можно рассмотреть инновационные технологии, в том числе и 3D-печать.
— Какими видятся перспективы неметаллической 3D-печати?
— Я смотрю с позитивом на всё многообразие АТ на российском рынке: и на керамику, и на полимеры, и на стекло, и на пластик. Изделия, напечатанные из поликарбоната или Ultem, в каких-то случаях не уступают по своим характеристикам металлически аналогам. Ведущие мировые компании уже сейчас задумываются о новых методах печати, о новых материалах. Один из наших партнеров, компания Stratasys, разработавшая в 1988 году FDM-печать, сегодня пробует инвестировать в новые технологии, позволяющие работать с огромным ассортиментом конструкционных пластиков и металлов. Высокая скорость изготовления серийных изделий (от нескольких десятков секунд до нескольких минут) и надежность 3D-принтеров — именно в этом направлении двигаются гиганты индустрии, они хотят поставлять оборудование для концернов авиационной, автомобильной промышленности, энергетики. Повторюсь, что мировое аддитивное сообщество активно погружается и в MIM-технологии, хотя они появились более 30 лет назад. АТ — технологии одной кнопки: нажали, ушли, получили результат. Но если раньше готовые изделия появлялись на следующий день, то сейчас производители стремятся к высокоскоростному выращиванию изделий, измеряемому часами или даже минутами.
— А как обстоят дела с отечественными порошками?
— Производить порошки для лабораторных испытаний могут многие российские профильные компании (например, ВИАМ). С промышленными объёмами дела обстоят гораздо сложнее. И надо сказать, что у каждого пользователя свои запросы и требования к порошкам. Например, «ОДК-Авиадвигатель» с помощью АТ решает задачу по ремонту изношенных лопастей турбин, и у них есть свой DMD центр. Но в любом случае новый порошок требует длительной обкатки и испытаний, здесь, как и с оборудованием, всё достаточно непросто. Но впадать в пессимизм не стоит, постепенно набирает обороты новый очень практичный тренд — использование проволоки для 3D-печати.
— Несмотря на трудности, мы пытаемся следовать за мировыми лидерами?
— Я ценю разработки отечественных ученых, они изобретают новые порошковые сплавы, в первую очередь для авиационной и космической отрасли. Безусловно, эти направления должны развиваться, но новые материалы требуют новых испытаний, новых режимов работы оборудования. Запад в основном делает ставку на решения, созданные много лет назад, тем самым делая 3D-печать более стабильной и предсказуемой.
— При том, что сегодня рынок предлагает широкий выбор хорошего импортного софта, некоторые отечественные компании пытаются сделать свой собственный софт для своих принтеров. У кого, на ваш взгляд, это действительно хорошо получилось?
— Для меня большая загадка, почему, например, генеральный директор ООО «Эксклюзивные решения» Денис Власов не может чувствовать себя уверенно на российском рынке. Имея огромный жизненный опыт инженера, разработчика и, наконец, ремесленника в хорошем смысле слова, чувствующего всю технологию на пальцах, Денис успешно разрабатывает не только собственное ПО, но и печатные платы, сканаторы, приводы. К сожалению, эта успешность пока сводится к созданию уникальных, крайне коротких по времени разработки, и с высокой долей «российскости» решений.
— Кстати, в своем выступлении на конференции он акцентировал внимание на модульном принципе построения отечественных 3D-принтеров, как одной из главных проблем российских производителей. Вы с ним согласны?
— Многие современные 3D-принтеры популярных технологий собираются по принципу конструктора ЛЕГО. Производители берут лазерный источник, выбирают среди двух или трех вариантов лазерных сканаторов, металлическую раму, корпус, приводы, затем всё это собирают и выдают за готовое решение. В итоге мы получаем черный ящик, в котором очень сложно отладить процесс построения деталей. В ВИАМе долгое время полагали, что движение лазерного луча постоянно, а оно, оказывается, дискретно. Специалисты института не могли этого знать по причине невозможности контроля некоторых параметров оборудования — они намеренно скрыты производителем. А Денис Власов начал разработку с нуля и принял решение развивать все компоненты своей аддитивной установки, пожалуй, кроме лазерного источника. В дополнение к этому нужно добавить замечательный пример стратегического мышления Дениса, который, пожалуй, первым среди российских разработчиков, предложил принцип печатающих ячеек, объединенных в Фабрику RussianSLM FACTORY. Компания «Эксклюзивные Решения» создаёт уникальную экосистему полностью подконтрольного производства и дает возможность всем клиентам получить доступ к каждому винту, к каждому параметру работы принтера. Однако, несмотря на свои замечательные продукты, Денис с большим пиететом относится к своим конкурентам — АО «Лазерные системы», считая их одними из лучших в России.
— Удивительно, что уникальный опыт ООО «Эксклюзивные решения» не тиражируется и не пиарится на государственном уровне, при том, что в России с высоких трибун раздается так много пафосных слов про импортозамещение и доверенные системы.
— В этом смысле история с 3D-принтерами аналогична той, что сложилась с оборудованием для классической металлообработки. Отечественные компании-потребители предпочитают приобретать иностранное оборудование, руководствуясь брендовой составляющей, и при этом не осознают, какие ограничения могут получить. Но смысл работать с отечественными производителями есть, даже если первый блин выйдет комом. Многое зависит, конечно, и от воли госструктур, просто не следует форсировать события, а реализовывать программу развития АТ в России поэтапно, что дополнительно подстегнет отечественных производителей совершенствовать собственную продукцию. Одновременно будет расти и развиваться клиентская база. Китайские компании буквально вынянчивают инновации на внутреннем рынке, а насытив его, они уверенно выходят на мировую арену. Что мешает нам поступать точно так же, ведь деньги в стране есть?
— Многие участники конференции говорили, что, по их ощущениям, государство, не увидев быстрого эффекта от внедрения АТ на промышленных предприятиях России, заметно ослабило к ним интерес. В то же время сейчас разрабатываются ГОСТы в этом сегменте, ведется работа над государственной стратегией развития АТ…
— ГОСТы практически переписываются с зарубежных аналогов, они ориентированы на технологии позавчерашнего дня. Работа в области стандартизации и нормативно-правой базы ведется очень медленно. Технический комитет по стандартизации «Аддитивные технологии» (далее — ТК 182) был создан в 2015 году, но пока результаты его работы не впечатляют. Госкомпании уже много лет демонстрируют свои проекты, но до серии пока дело не дошло. Как показывает практика, изготовить опытный образец — не самая сложная задача, гораздо труднее обеспечить надежность и повторяемость, чтобы каждый последующий принтер не отличался от предыдущего. Это другие деньги и совсем иной уровень производства.
— Дмитрий, в заключение нашей беседы расскажите о тех направлениях, где аддитивные технологии активно применяются и продолжают наращивать своё влияние, а также о перспективных точках роста.
— Традиционная сфера применения АТ, куда инвестируются огромные деньги, — авиация и космос. Развивается сегмент машиностроения и энергетики. В ближайшем будущем крайне перспективным рынком станет нефтегаз. АТ продолжают успешное развитие в здравоохранении, особенно в стоматологи, травматологии. Другое дело, что для медицины эти технологии тяжеловаты и сложны: врачам никак не разобраться в них без помощи инженеров и сервисных провайдеров. Очень сильно выручает аутсорсинг. На сегодняшний день практически во всех сферах человеческой деятельности примериваются к АТ. В вопросах прототипирования у 3D-принтеров нет конкурентов. Я постоянно штудирую довольно много литературы, посвященной аддитивным технологиям, и часто наталкиваюсь на статьи, посвященные замещению традиционных способов производства 3D-печатью. Самые оптимистичные источники заявляют, что полная экспансия произойдет к 2030 году, однако, по ощущениям, замещение традиционных способов производства случится гораздо позднее и затронет в первую очередь сектор токарно-фрезерного оборудования. Но пока 3D-печать проигрывает по скорости и частично по качеству штамповочному и токарно-фрезерному производству. АТ на данный момент подходят исключительно для сложных эксклюзивных изделий. И всё же, несмотря на аморфность рынка АТ в России, в ближайшие 2-3 года мы увидим инновационные проекты, которые определят будущее 3D-индустрии.
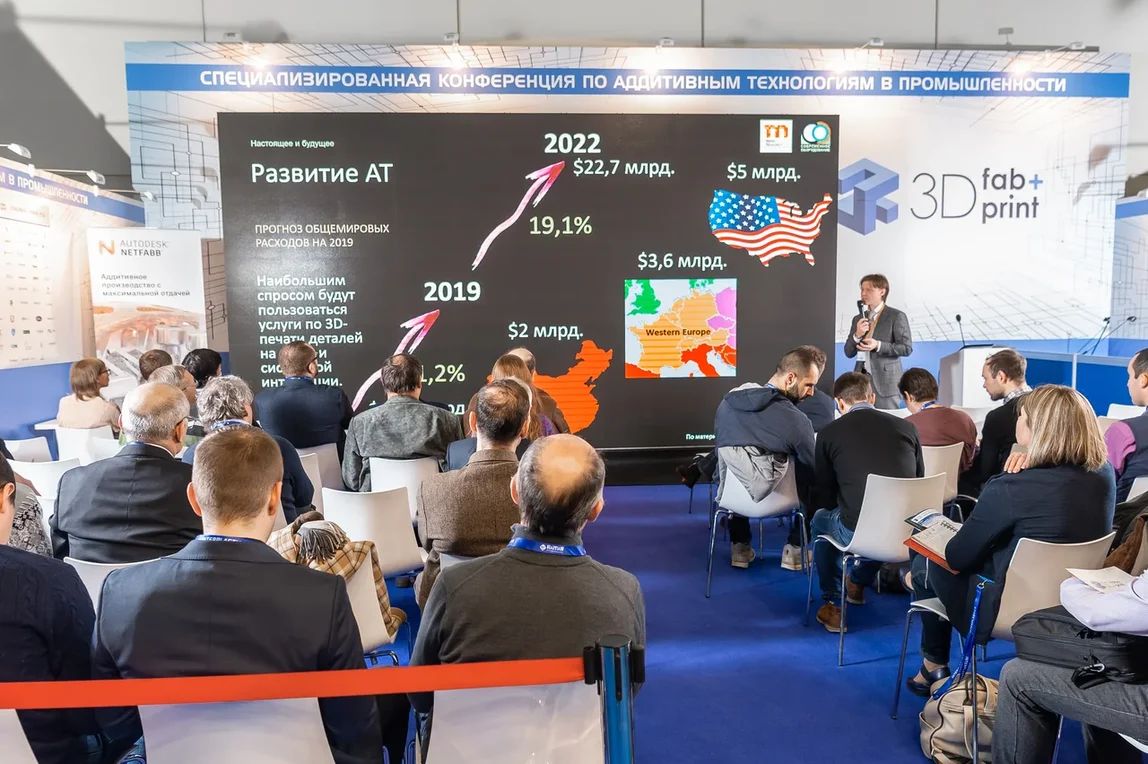
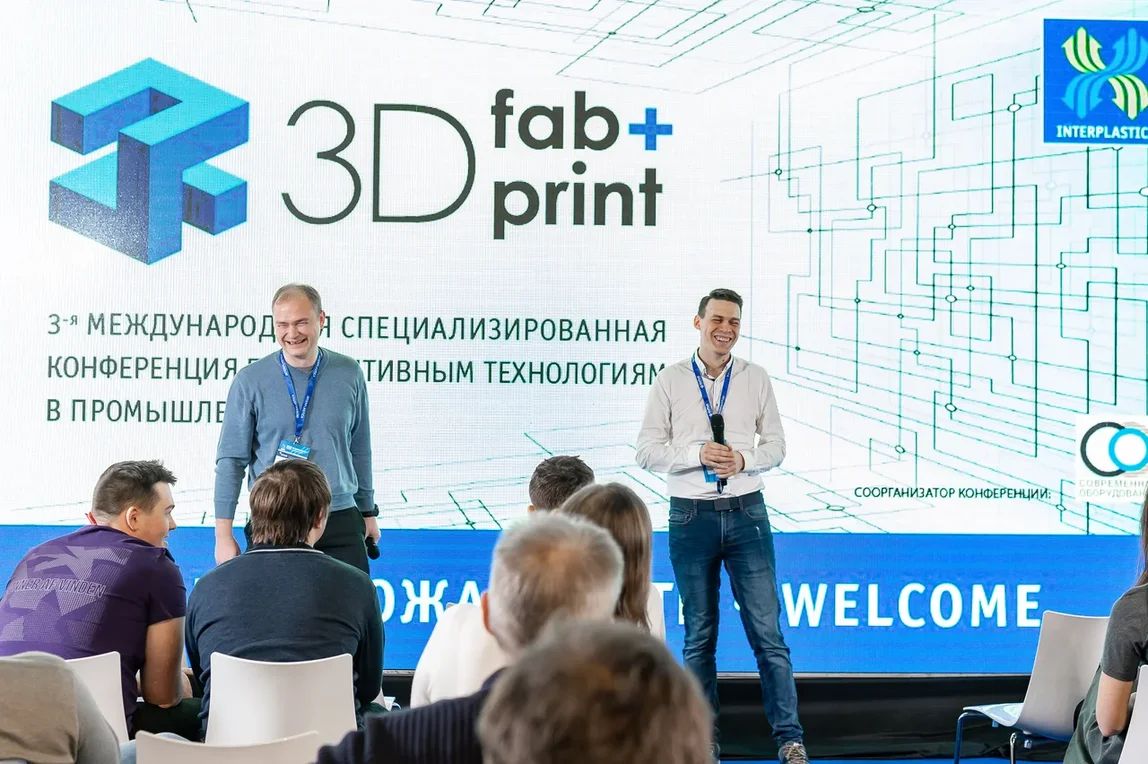
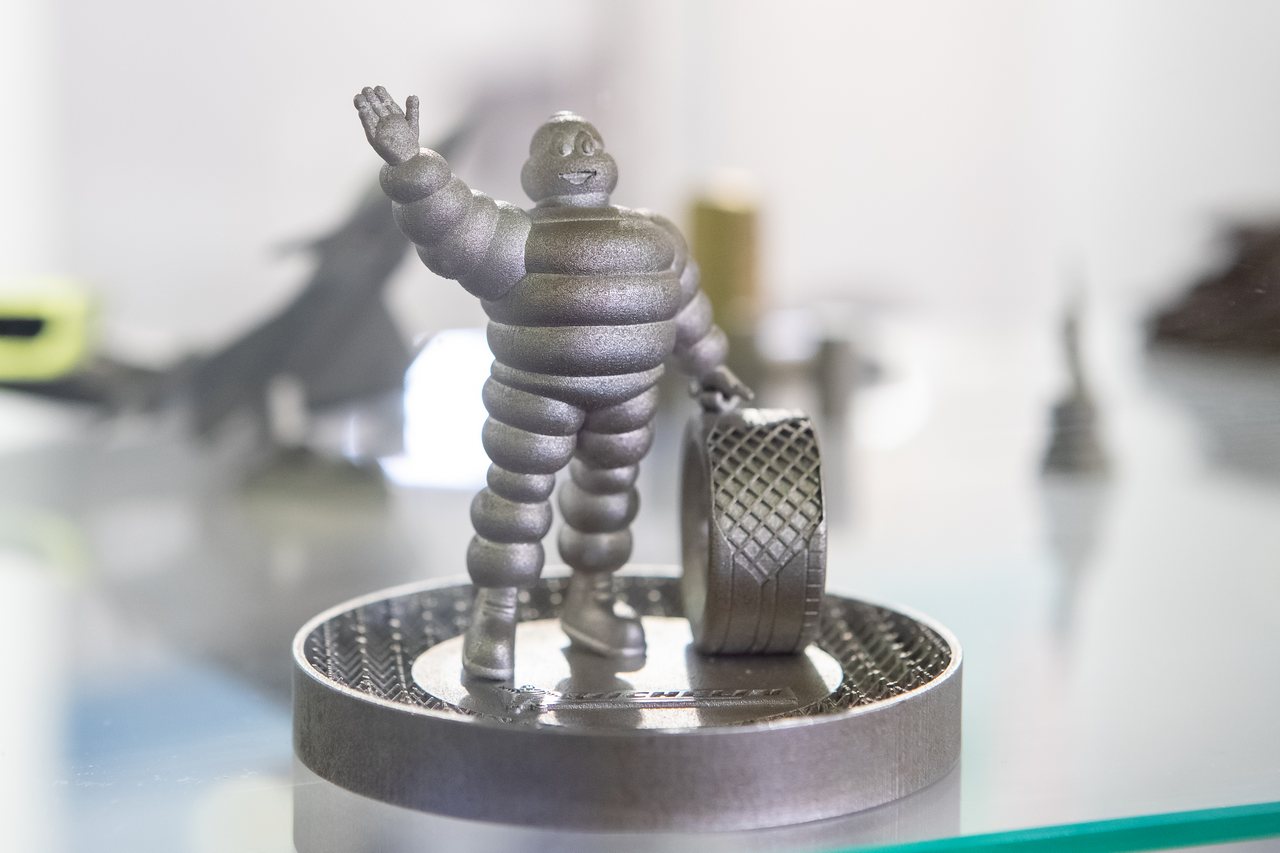
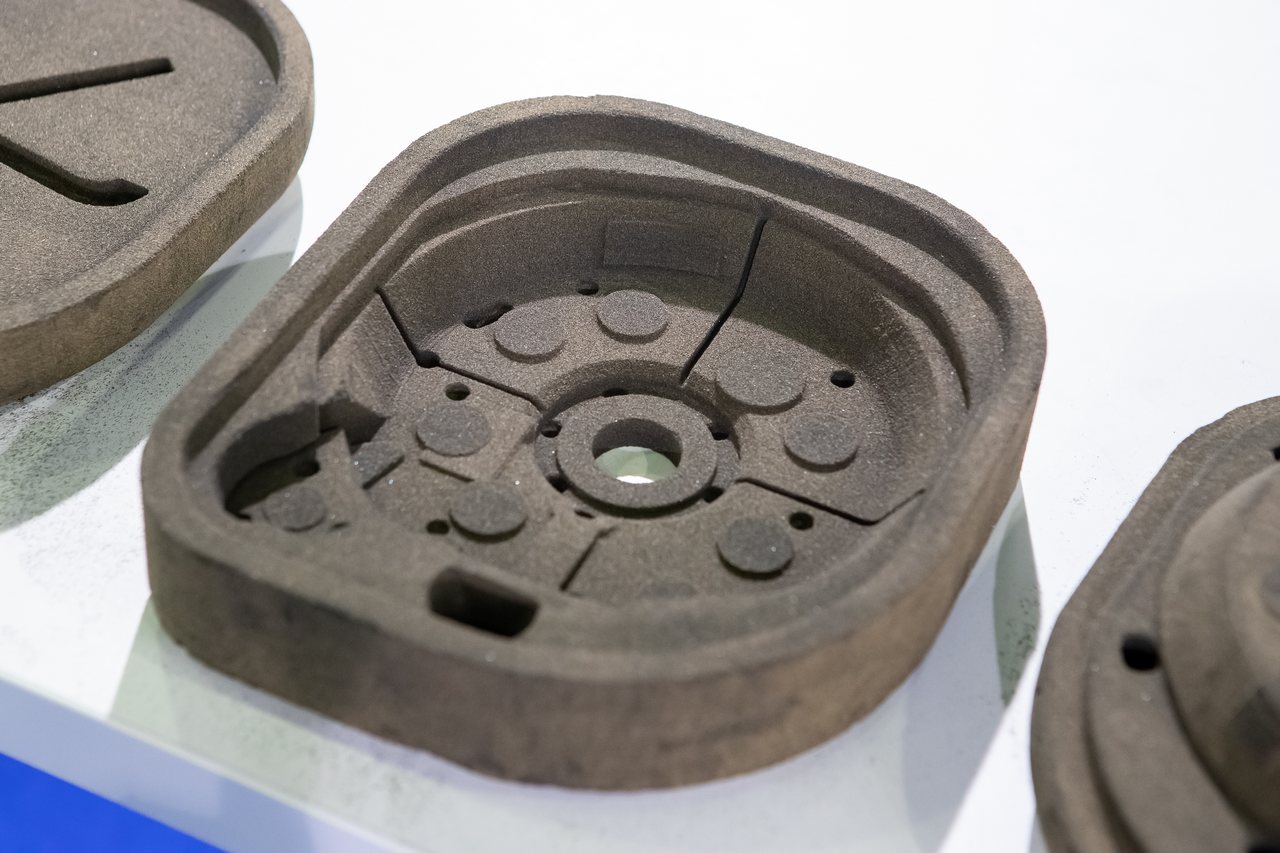
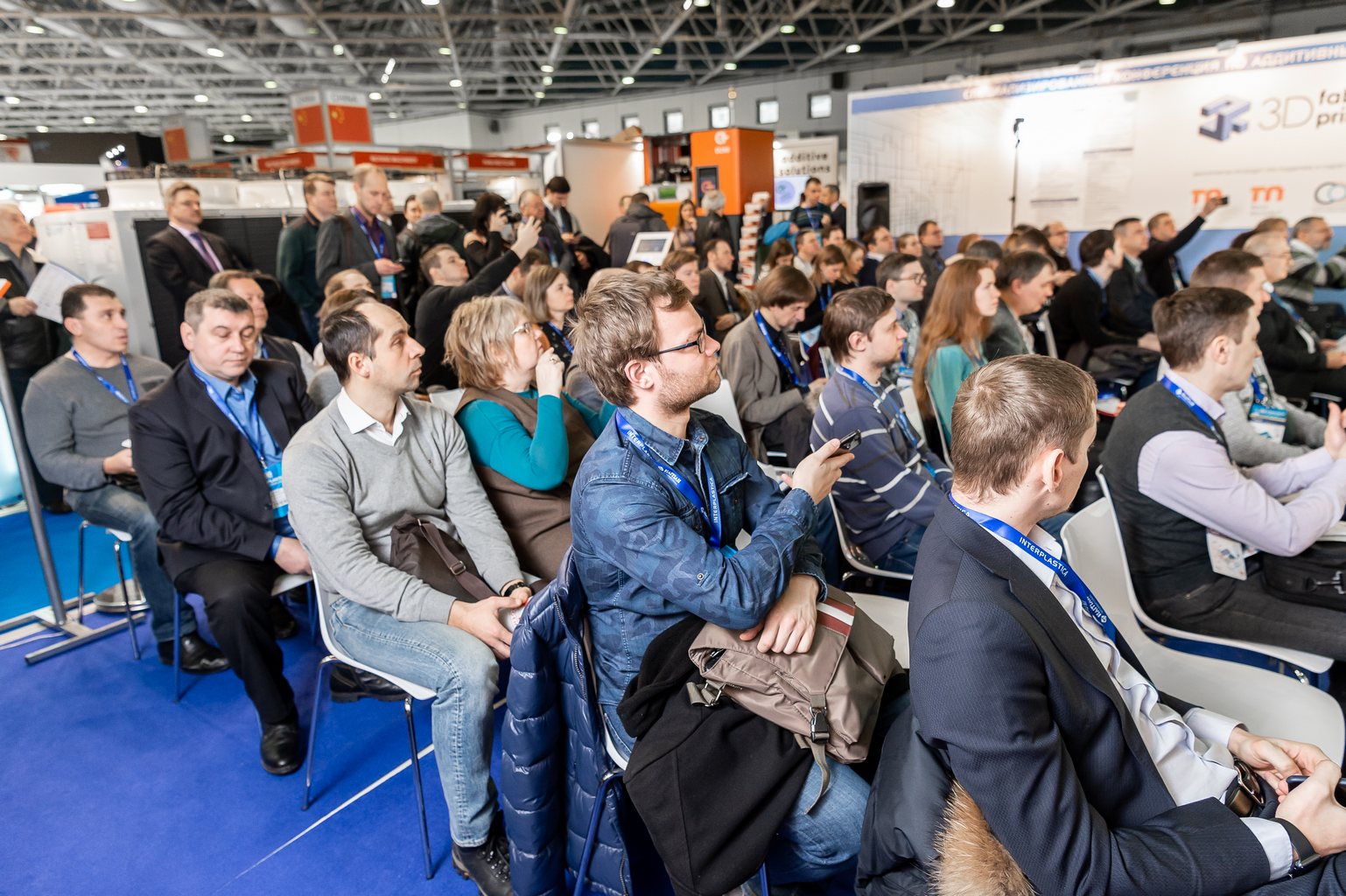
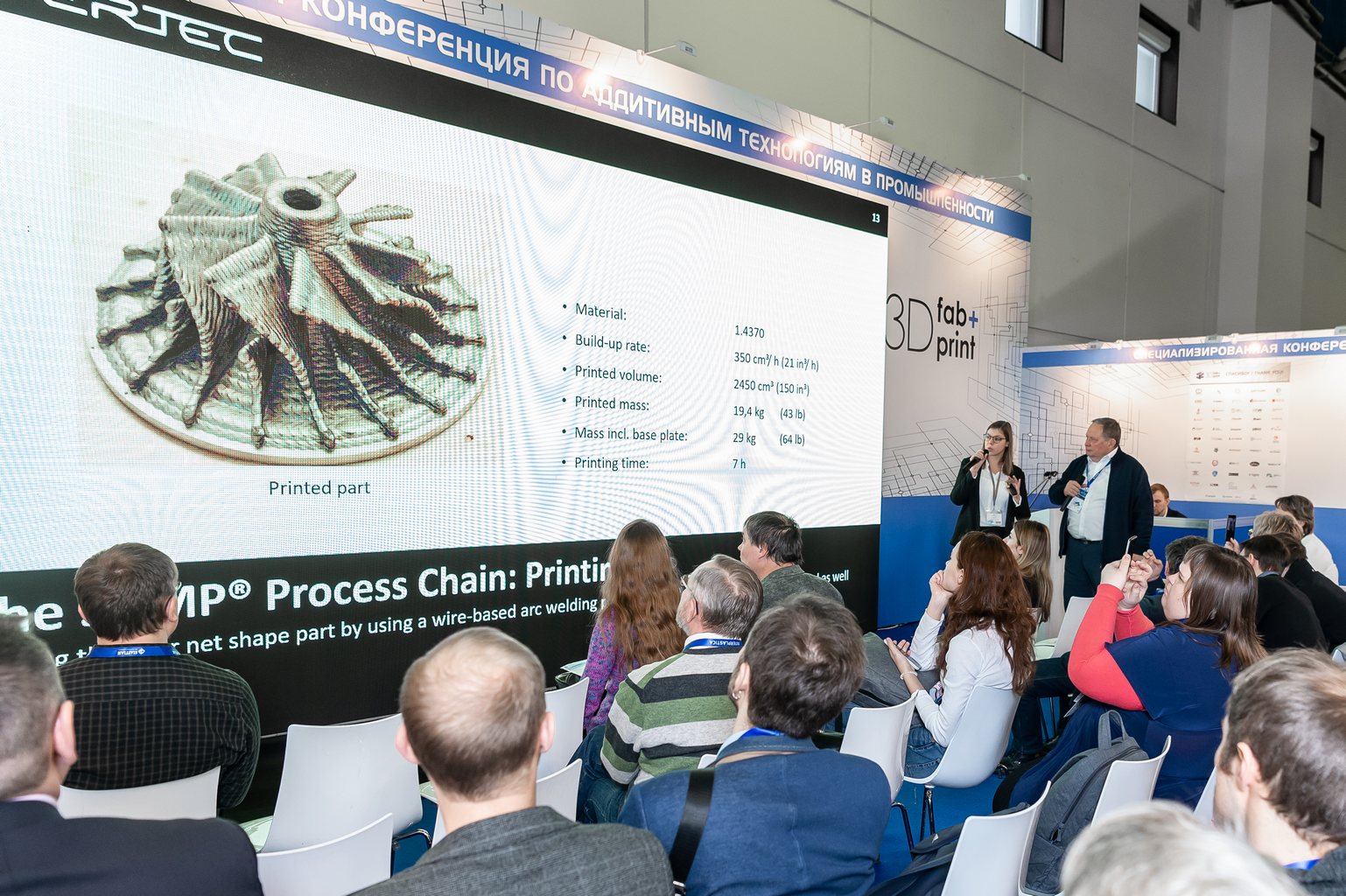
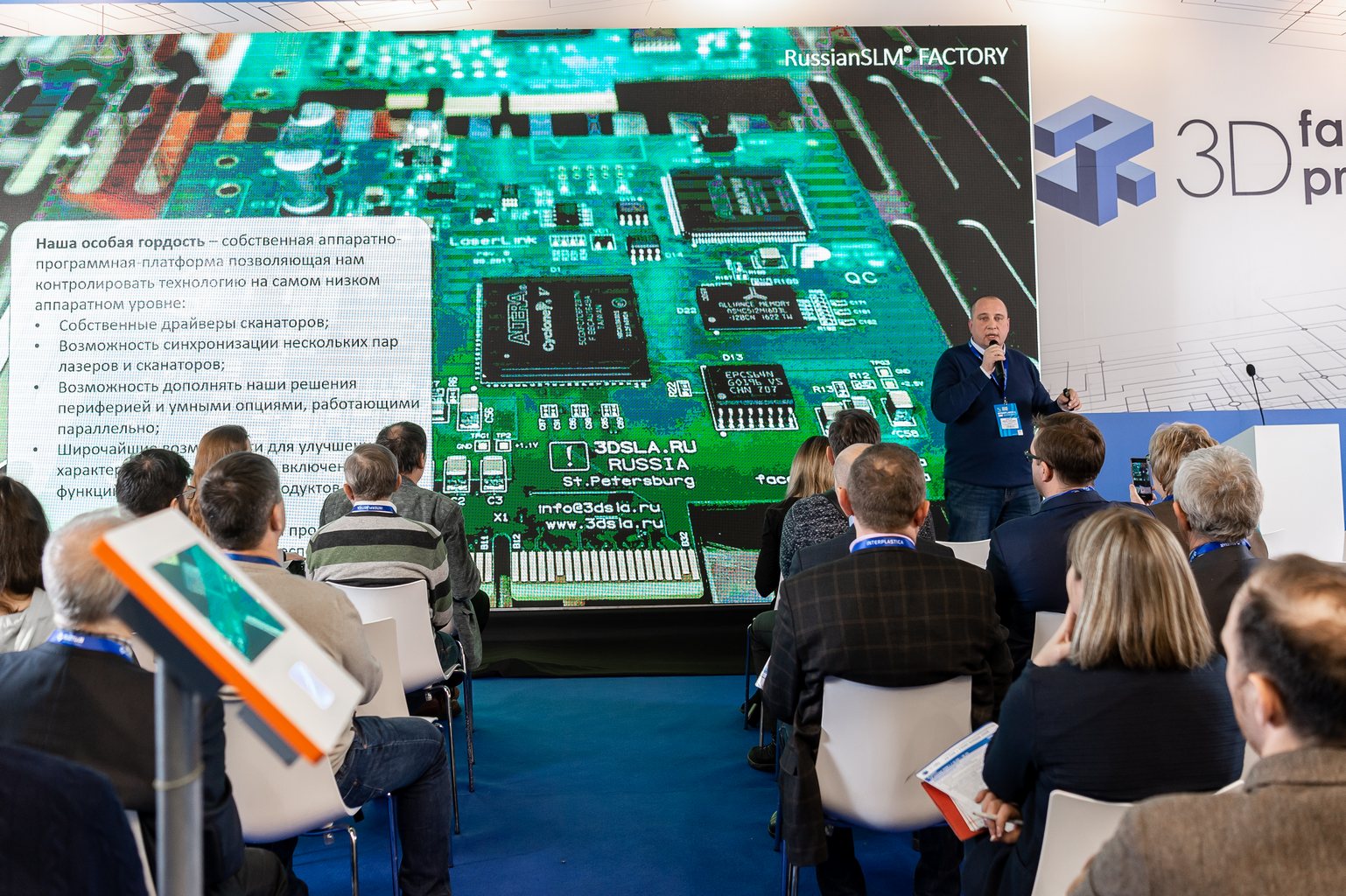
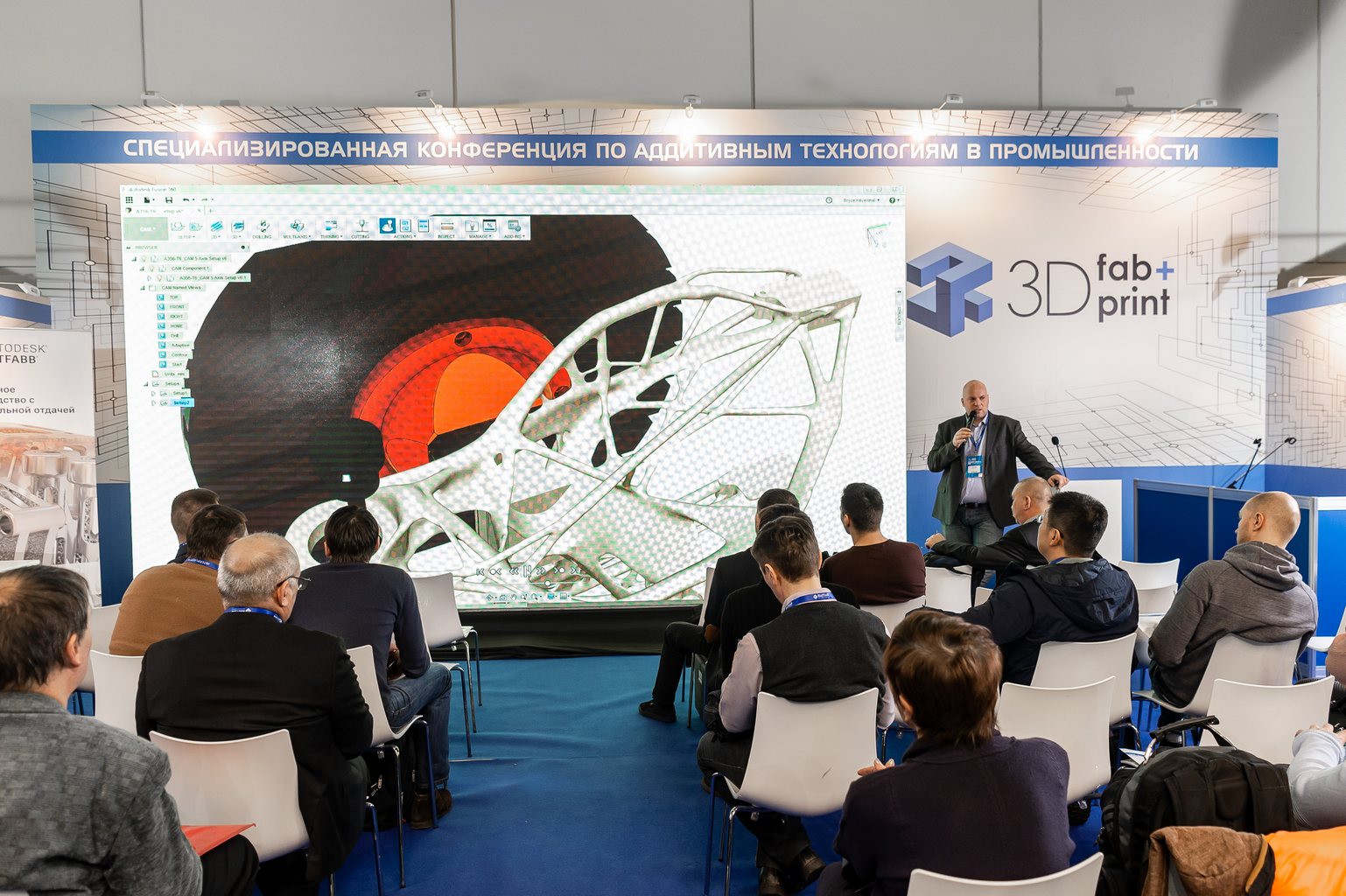